一、生产线构成
原料预处理系统
配备废钢破碎、清洗和分选设备,确保原料纯净度。部分生产线采用磁选技术去除杂质,提升原料利用率。
熔炼与雾化系统
核心设备包括电弧炉或中频感应炉,熔炼温度可达1600℃以上。雾化装置采用高压水或气体离心雾化技术,将熔融钢水快速冷却成微米级颗粒。
热处理与筛分系统
热处理设备包括淬火炉和回火炉,通过精确控温实现钢丸硬度与韧性的平衡。筛分系统采用多层振动筛,按SAE标准将钢丸分为11个等级,粒度范围覆盖0.1mm-3.0mm。
除尘与环保系统
配置脉冲布袋除尘器,废气排放符合国家环保标准。部分生产线采用封闭式生产,粉尘回收率超99%。
二、工艺流程
原料准备
废钢经破碎、清洗后,按比例添加铬、钼等合金元素,提升钢丸耐磨性。
熔炼与雾化
熔融钢水通过高压水雾化或离心雾化形成球形颗粒,表面粗糙度Ra≤3.2μm。
热处理
淬火温度880-920℃,回火温度400-500℃,确保钢丸硬度HRC40-50,冲击韧性≥8J/cm²。
筛分与包装
钢丸经振动筛分级后,采用吨袋或铁桶包装,净重误差≤±0.5%。
三、技术特点
高效节能
自动化生产线产能达5-20吨/小时,单位能耗较传统工艺降低15%-20%。
质量稳定
粒度偏差≤±5%,硬度偏差≤±2HRC,使用寿命较普通钢丸延长25%-30%。
环保达标
粉尘排放浓度≤10mg/m³,噪音≤85dB(A),符合ISO14001环境管理体系。
四、应用领域
表面处理
用于船舶除锈、钢结构防腐、汽车零部件抛光,清理效率较钢丝切丸提升30%。
喷丸强化
在航空发动机叶片、风电齿轮箱等高强钢部件中,可提升疲劳寿命1.5-2倍。
铸造清砂
适用于复杂铸件(如发动机缸体)的精密清砂,表面粗糙度可达Ra1.6μm。
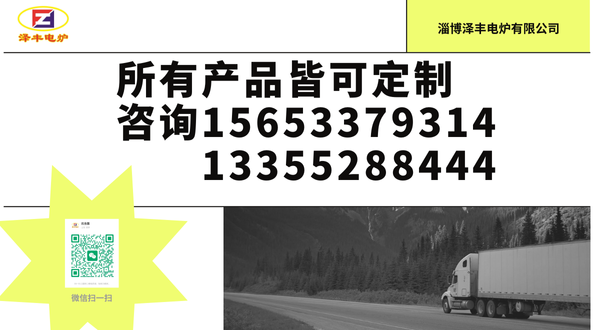